Production process automation
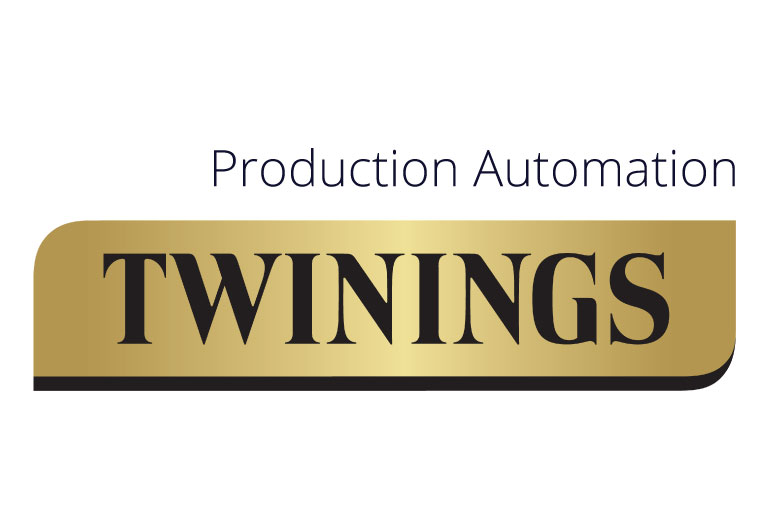
Products & Services taken
Self-developed framework by ARP Ideas
.Net core implementaton
Angular frontend
UI optimised for mobile devices
Integration with Active Directory
Company Overview
The Twinings company was founded in 1706 in London and is one of the largest food companies in Europe. Polish factory located in Swarzędz, Poland started production in 2011 and is one of the most modern, automated production plants.
The Twinings brand is well known to consumers of teas and herbal infusions, and the most famous blends include: Earl Grey, Lady Grey, English Breakfast. At the factory in Swarzędz, are produced over 400 different tea blends and the range is constantly expanding the wide range of our products. Currently, Twinings distributes products to nearly 120 countries worldwide.
Challenge
There are three production areas at the factory in which employees operate with raw materials to create different tea products according to the orders. Different tea blends are produced on the same machines, therefore, a solution had to be developed to avoid mistakes during the production of individual mixtures.
The company needed a system that could oversee and guide employers during all production stages, from creating a work order to ready-for-shipment processes.
Approach
The development of such a complex system needs to be appropriately organised and planned. First of all, we deeply studied all the production stages to find weak points. Then, in cooperation with Twinings, we’ve developed a detailed production scheme and approved all the processes that needed to be automated.
The plan was to create a system to track employees' actions and product movement during production. Every raw material item and production point is marked with specific barcodes that employees should scan to complete tasks created by the system.
The process starts when the manager places the order, then the system checks production machines on queues and updates them. Machine queues must be updated according to the blend matching matrix that was created to avoid mixing specific blends. After this, production starts and dedicated employees receive automatically created tasks, for example, moving raw material to the production lift or filling the machine with raw material. The tasks are created during all production cycles until ready for shipment product is placed in the warehouse area. Due to the scanning system, production is tracked at every stage, and blend mistakes are minimum.
Solutions
Tracking system for handscanners that automatically create tasks according to employees' actions.
Machine queue system that tracks which raw materials are used to avoid spoilage of tea blends.
The system core was designed on a custom Framework developed by ARP Ideas.
System Authentication uses Active Directory.
All tracing data is stored in SQL Database.
Next Steps
Expand the system to work with warehouse processes. Operation of transition machines that should feed the right car with ready-to-ship tea pallets.
Integration with AGV forklifts that operates without workers.
Outcomes
Dropped the number of issues of wrong blends by 95%.
The production process System started to work smoother.
Management can easily track all the processes and status of the orders.